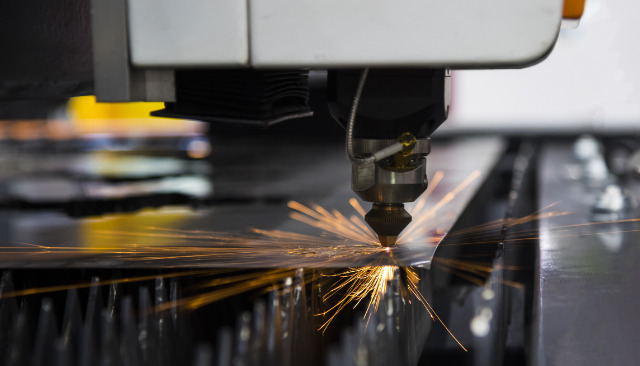
The Sheet Metal Hydroforming Process
When the right situation presents itself, sheet metal hydroforming will be an efficient and cost-effective manufacturing process. However, the situation will depend on the project and the type of equi …

The Sheet Metal Hydroforming Process
When the right situation presents itself, sheet metal hydroforming will be an efficient and cost-effective manufacturing process. However, the situation will depend on the project and the type of equi …

What Is Hydroforming And How Can It Help You?
When discussing hydroforming with some who has never heard of the process, the obvious question that will arise is: what is hydroforming?
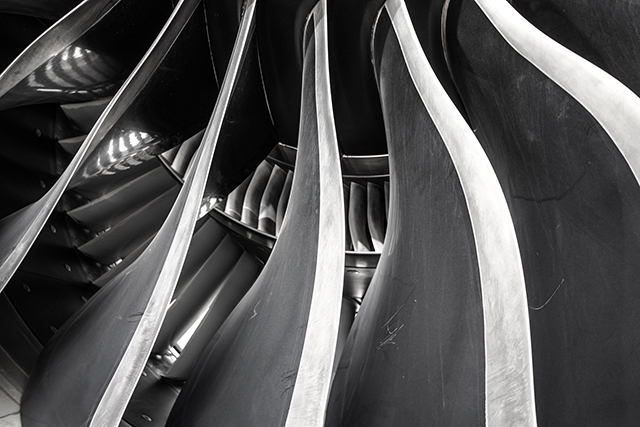
What Is Hydroforming? An Explanation from American Hydroformers
Have you been looking for a cost-effective way to form your ductile metals into parts that are not only structurally firm but have strong parts? One of the best methods you can use in this industry is …
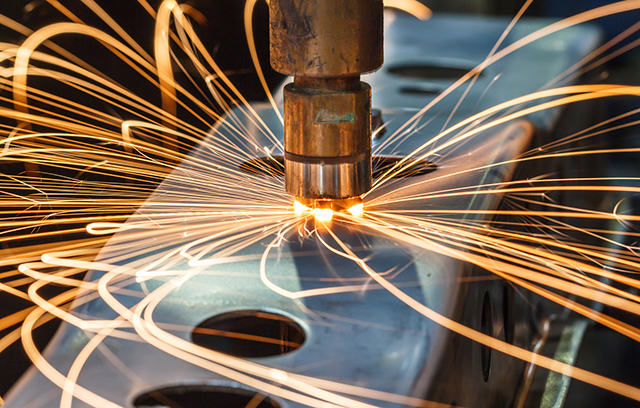
What Is Hydroforming: Sheet Metal Hydroforming
Metal hydroforming is not anything new, but it does offer an appropriate alternative that some manufacturers may not be considering. If your organization or company does not currently own any hydrofor …

Tube Hydroforming vs. Sheet Hydroforming: What is Hydroforming?
What is hydroforming? Hydroforming is when the force of water, hydraulic fluids, or oils is used to shape a single part. There are two types of hydroforming and each has uses when creating products fr …

Tube Hydroforming Process Leads to Amazing Bicycles
Though tube hydroforming has humble roots, it has taken those roots and firmly planted them in industry, design, and innovation. For instance, take a look at how much innovation has gone into bikin ...

Deep Draw Hydroforming Process
What is Sheet Metal Hydroforming? Sheet metal hydroforming is a metal forming process that is achieved by applying force to sheet metal to alter its overall geometric shape as opposed to added or sub ...

Deep Draw Hydroforming Explained
In the metal forming industry 'hydroforming' has become somewhat of a buzzword and general term for metal shaping. But there are many ways of shaping metal in this industry, all with their own unique ...
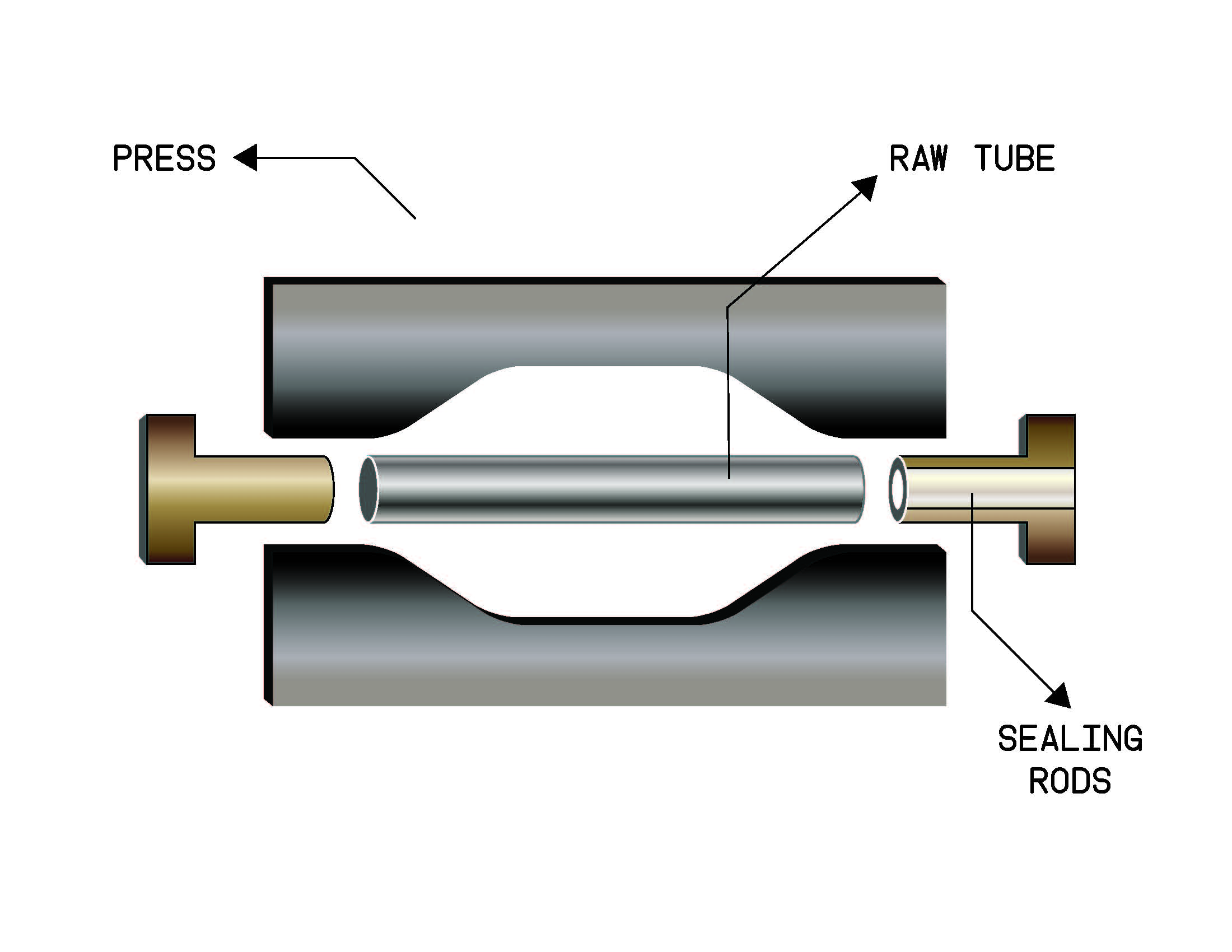
What is Tube Hydroforming?
Often, when it comes to discussing what we do, the very first question asked is: What is tube hydroforming? The simplest answer is that hydroforming is a way to shape metal. This cost-effective proces ...